Model NO.: GX--EPEG105
Condition: New
Main Raw Material: LDPE
Foaming Agent: Freon or Butane
Capacity: 1000-3000kg/24 Hours
Products Diameter (Pipe): 20-100mm
Products Diameter (Rod): 20-80mm
Products Length: User Defined
Foaming Ratio: 20-40
Installation Power: 110kw
Power Supply: 380V 50Hz
Dimension Size: 23 X 2.3 X 2.2 M
Transport Package: Standard Package
Origin: China
HS Code: 8477209000
Model NO.: GX--EPEG105
Condition: New
Main Raw Material: LDPE
Foaming Agent: Freon or Butane
Capacity: 1000-3000kg/24 Hours
Products Diameter (Pipe): 20-100mm
Products Diameter (Rod): 20-80mm
Products Length: User Defined
Foaming Ratio: 20-40
Installation Power: 110kw
Power Supply: 380V 50Hz
Dimension Size: 23 X 2.3 X 2.2 M
Transport Package: Standard Package
Origin: China
HS Code: 8477209000
 - PRODUCTION FEATURES & APPLICATIONS
 EPE foamed pipe is a kind of new-type foaming material and it is widely used in the insulations of air conditioner sheath, pipeline heat insulation, toy guardrail, recreation places, etc. Due to its good foaming, elasticity and heat preservation.
 As a kind of new-type filling ornament material, EPE foamed stick/profile is widely used in the stereotype, filling and ornament of spring mattress , sofa stem and edge, automobile seat ,sofa backrest and top-grade clothing. It is also widely used in the filling of contraction joint in building due to its good rebound elasticity.
3.General characteristics:
 -- polyethylene based products-inert material, highly resistant to chemicalsÂ
 --environmental friendly products
--100% recyclable
--flexible low weight material, easy to slip and installÂ
 --low thermal conductivity
 --compatible with all sealing materials
 --fine round closed-cell cellular structure assures: negligent absorption and water permeability
 --excellent impact and compression resistance even for low thickne
4.  Equipment Device List
- Blender mixer                                                         1 unit
Hopper capacity | 100 KG |
Mixing material motor | 1 unit 4 pole 3KW |
2.Automatic feeding device system
Loading material motor | 1 unit 6 pole 1.1KW |
 Automatic controlling system |  Timing quantitative feeding |
3. Extruder  1set
3.1>Screw and cylinder | Â |
Screw diameter                 |   105mm |
L/D | 55:1 |
Screw speed  | 10-50shift/minute |
Screw and cylinder material | 38CrMoALA superior alloy steel,by nitriding treatment,hard chrome plating |
3.2>Main drive motor  frequency control | 1 unit |
Driving power  | 45KW |
3.3>Reduction gears Hard tooth surface dedicated |
1 unit |
3.4>Electrical appliance control cabinet anti-explosion, contactless warming | 1 unit |
3.5> heating method | cast aluminium heating ring |
Heating power               |
40KW |
Heating zone | 10 zones Intelligent automatic constant temperature control |
3.6>Cooling method | Water circulation cooling |
- Foaming agent injection system
Injection device        |  plunger type metering pump 1 unit |
Injection mode | high pressure injection |
Injection pressure | 10-30Mpa |
Driving mode | explosion proof motor |
Driving power | 3KW |
Injection volume   | 10-60L |
5.Monostearin heating Injection system
Injection device | plunger type metering pump 1 unit |
Injection mode | high pressure injection |
Injection pressure  | 10-30Mpa |
Driving motor | 1 unit |
Driving power | 0.75KW |
Heating power | 2KW |
Injection volume | 5-25L |
Melting pot volume |  15L |
6.Extrusion die head and mould
Mould material |
High quality forging mold steel  |
Shape  | circular expansion die head |
Mould  | 1 unit(user defined ) |
Heating method | cast aluminium heating |
Heating power           |  4KW |
Heating zone  | 2 zones, automatic constant temperature |
Pressure Gage | 1 unit |
- Cooling and forming system Â
7.1> Air ring | 1 set |
Fan | 1 set |
Motor | 0.37kw |
7.2>Bellows | 2set |
Fan | 3set x2 set |
Motor | 0.3kw x6 |
8.Hauling-off system           1 unit
Hauling-off roller   | 1unit |
Hauling-off speed                | 30-60m/minute |
Motor                         | 1unit 4 pole 3KW |
Turbine speed reducer          | 1 unit |
Meter counter | 1 unit |
Warning system                 | 1unit |
9.Cutting system     Â
Cutting system | Fully-automatic cutting |
Motor | 1set 1.1kw |
- Blank system
Blank system | Fully-automatic |
Count system |
Fully-automatic  |
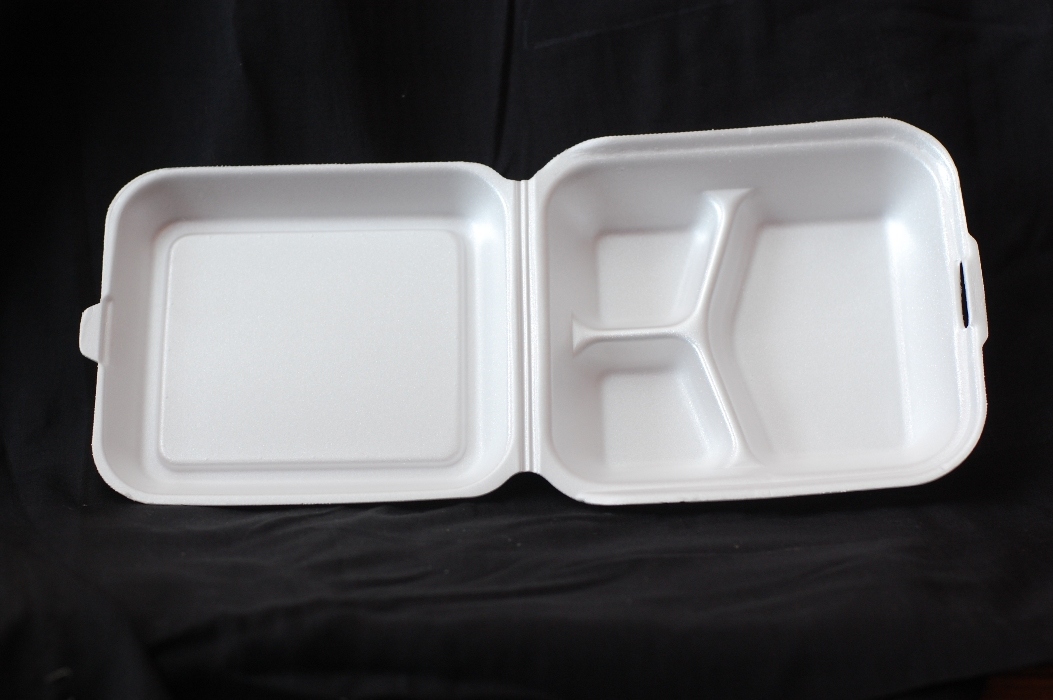
PS foam food box making machine, use the PS foam sheet made by the PS foam sheet extruder, as the materials.
throught changing the different molds to get the various kinds of colorful products, like the PS foam food box, PS foam food tray, egg tray, bowl, cake case, fruit tray, and absorbent tray to contain the meat, or fish or shrimp,etc,.
which is used for package industry.
Â
GENERAL INFORMATION:
Â
Â
Â
Raw material:Â |
PS granule, talc, butane and so on.   |
Finished products:Â |
Ps foam fast food box, foam tray, pizza box, hamburger, egg tray, and so on. (Depending on changing mold)Â Â Â Â |
Sheet thickness: |
1-5mm |
Sheet width:Â |
600-1200mm |
Capacity:Â Â |
180-240kgs/h |
Operator: |
6-8 workers |
Water consumpation:Â |
200kgs/24hrs |
Cooling water tower:Â |
20 T/ h |
Butangas consumption:Â |
45-50 kgs/one ton materials (based on the foam ratio range from 16-20) |
Air compressor : |
1.5 m3/min |
Installation power: |
550Kw |
Power supply : |
3 phase 4 line 380V 50Hz |
Work shop area:Â |
PS Foam Sheet Extrusion Line workshop: 25x8x4m (L*W*H) Fully-automatic Vacuum Forming Machine workshop :20x8x4m  |
Warehouse: |
Per raw material warehouse area 60M2 (at least) Per finished products warehouse area 60M2 (at least) Â |
Container |
3x 40'HQ containers |
Each factory has its respective advantage about what they done , and each manufacturer is good factory, which is the truth, and we believe it.
While here is us , Yantai gossie be your nice choice.
Â
Main equipment and technical parameter
1). GX- 105/120 PS Foam Sheet Extrusion Line
1). GX- 105/120 PS Foam Sheet Extrusion Line
Components: |
 |
A.Mixer |
 |
Hopper Capacity |
300-500kg/ hopper (controlled by time relay) |
Motor |
1 set, 4-pole, 3kw |
B. Automatic Feeding System |
 |
Automatic Self-control System |
 |
Motor |
1 set, 6-pole, 1.1kw |
C. NO.1 Extruder |
 |
Screw Diameter |
Φ105mm |
L/DÂ Â Â Â Â Â Â Â Â Â Â Â Â |
30:1 |
Screw Material: |
38CrMoAlA adopt Nitrogenous treatment |
Heating zones: |
6 zones |
Butane Pump: |
1 set |
Digital Pressure Gauge: |
1 pc |
Fully-automatic Hydraulic filter changer: |
1 set |
Electrical Cabinet: |
1 set |
Motor: |
3 sets (4-pole, 55kw,by frequency exchanger) (4-pole, 2.2 kw, by frequency exchanger ) (4-pole, 5.5kw) |
D NO.2 extruder |
 |
Screw Diameter. |
Φ120mm |
L/DÂ |
32:1 |
Material |
38CrMoAlA adopt Nitrogenous treatment |
Heating zones |
6 zones |
Pressure gauge |
1pc |
Automatic water cooling system |
5sets |
Motor   |
4-pole 55kw by frequency exchanger |
E. Cooling System |
 |
Hollowness water circulation cooling |
1 set, as the dimensions by the customers |
F. Hauling-off System |
 |
Rubber Roller |
3 pcs, (according customer's requirment) |
Traction Speed |
3-31m/min |
Motor |
1x 4-pole, 3 kw (controlled by frequency changer) |
Counter  |
1pc |
Alarm system |
1set |
Haul-off type |
run in S route by self-friction |
G. Winding Device |
 |
Winding Pneumatic Shaft |
2 pcs (according customer's requirment) |
Torque motor |
2sets |
Turbine Reducer |
2sets |
Static Electricity Eliminator |
1set |
Alarm |
1set |
H. Die Material |
 |
Installation Power |
200kw |
Central height |
1000mm |
I. Weight |
8 T |
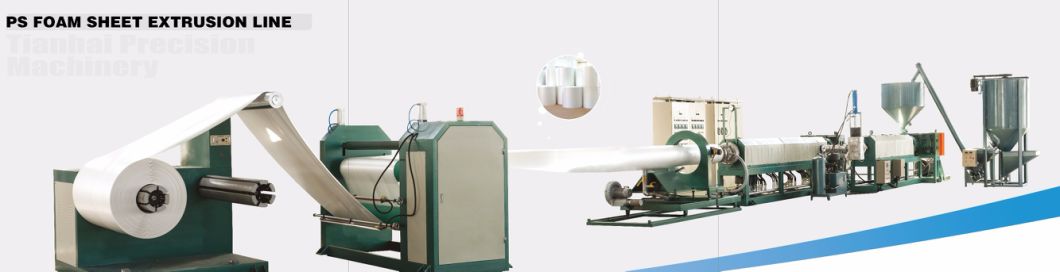
Â
2) GX-1100x1250 Fully-automatic  Forming Machine (with Crusher in line)
A.Technical data:
Â
A.Technical data:
Â
1.Control system |
 |
Automatic Control Cabinet |
1 set |
automatic Temperature Control Cabinet |
1 set |
PLC controller |
Adopt Emerson USA |
Touch screen |
Adopt Taiwan Weinview |
 |
 |
2.Automatic Pneumatic Feeding device |
1 set |
 |
Feeding length can be adjusted. |
 |
 |
3.Heating System, |
2sets |
Subsidiary Heating Zone /2 sets |
Adopt the far infrared radiation tile. |
 |
 |
4. Forming System |
Adopt hydraulic cyclinder drive |
Motor |
2 sets 7 kw |
Hydraulic stations |
2 sets |
Vacuum forming press |
60T. |
Forming area |
1040mm×1250mm |
Vacuum forming speed |
3-4s/mould. |
 |
 |
5.Cutting off System |
Adopt hydraulic drive |
Motors |
1 set 7.5kw |
Hydraulic station |
1 set |
Max. Punching |
100T |
Cutting off area |
1040mmx1250mm |
Cutting off speed |
3-4 s/mould |
 |
 |
6.Stacking System |
 |
Robot manipulator |
Servo motor control, Japan Omron Bran
Aquajet series are turbine-driven machines designed for fully mechanized and labor-saving irrigation. The main component parts such as turbine, automatic layering mechanism and crop-protecting sprinkler balancing mechanism enjoy the international patents and keep being updated. Aquajet provides the following additional features. Hose reel irrigation Aquajet 85mm Agricultural Irrigation Equipment,Farm Sprinkler System,Water Saving Hose Reel Irrigation,Travelling Sprinkler Irrigation System Shandong H.T-BAUER Water and Agricultural Machinery & Engineering Co., Ltd. , https://www.ht-bauer.com |