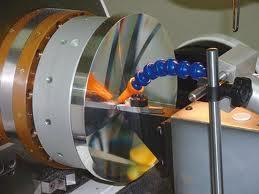
In the gear processing process, advanced blank forming process, stable and precise heat treatment process, and appropriate surface hardening process are the key factors for the final formation of gear products. For example, in the grinding process, there are several key steps: By using a grinding wheel with sharp edges and grinding the surface with small stress, the grinding feed can be increased, the grinding time can be shortened, the grinding efficiency can be improved, and the dressing of the grinding wheel can be extended. The spacing to reduce costs; by using appropriate grinding and dressing wheel parameters, to ensure that there is no grinding burn cracks and ensure the quality of the premise, use the highest possible grinding parameters to shorten the grinding time, improve grinding efficiency , To increase the output and ensure the accuracy and reduce the surface roughness; By using suitable grinding oil, under the premise of good lubrication and rust prevention, it is beneficial to reduce the surface stress of the grinding tooth surface, to avoid burn cracks, and to reduce the roughness. Decrease the degree of blocking the porosity of the grinding wheel to ensure the sharpness of the grinding wheel, reduce the dressing of the grinding wheel, reduce the amount of grinding wheel and reduce the cost.
In short, in the process of casting gears, we must pay attention to all kinds of problems in the design and processing, so as to ensure the quality of gears produced by casting.
Tungsten carbide grits are small particles or granules of tungsten carbide, a compound made up of tungsten and carbon atoms. They are extremely hard and have a high resistance to wear and abrasion, making them useful in a variety of industrial applications.
Tungsten carbide grits are often used as abrasives in cutting tools, grinding wheels, and sandpaper. They can also be used as an additive in metal alloys to improve their hardness and wear resistance. Additionally, tungsten carbide grits are used in the mining and drilling industry for rock drilling and excavation.
These grits are available in different sizes and shapes, such as spherical or irregular particles, depending on the specific application. They are typically produced through a process called sintering, where Tungsten Carbide Powder is heated and compressed to form a solid material.
Overall, tungsten carbide grits are highly valued for their hardness, durability, and resistance to wear, making them essential in various industries where high-performance materials are required.
Tungsten Chips,Tungsten Carbide Chips,Tungsten Carbide Grits,Tungsten Carbide Fragments
Luoyang Golden Egret Geotools Co., Ltd , https://www.xtcthermalspray.com